In order to have good quality control and assurance, machine calibration and periodical maintenance are essential components of good quality control and assurance in the manufacturing industry.
Here’s why they are important:
Accuracy & Precision
Accuracy & Precision
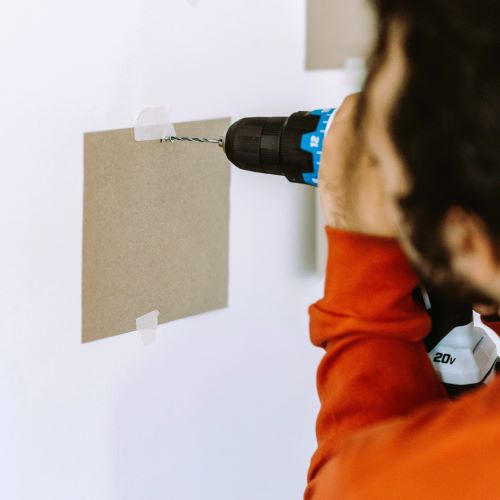
Machine calibration ensures that manufacturing equipment, such as measuring instruments, CNC machines, and robots, is set to perform with accuracy and precision.
When machines are properly calibrated, they produce products that meet design specifications, reducing errors and defects.
Consistency
Consistency
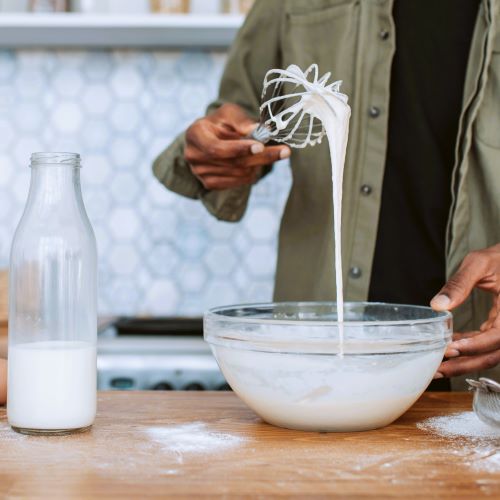
Calibration helps maintain consistency in the manufacturing process. It ensures that machines produce the same results over time, which is crucial for quality assurance.
Consistency is a key factor in meeting quality standards and delivering products that consistently meet or exceed customer expectations.
Compliance
Compliance
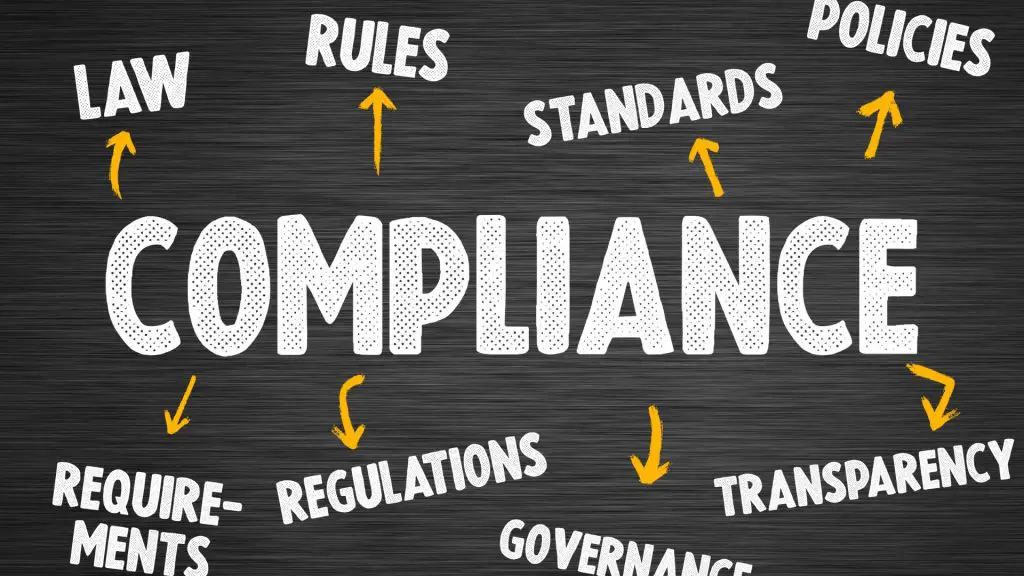
In many industries, compliance with regulatory and quality standards is mandatory.
Proper calibration is necessary to meet these standards. Failure to comply with regulations can result in legal and financial penalties.
Reduction of Variability
Reduction of Variability
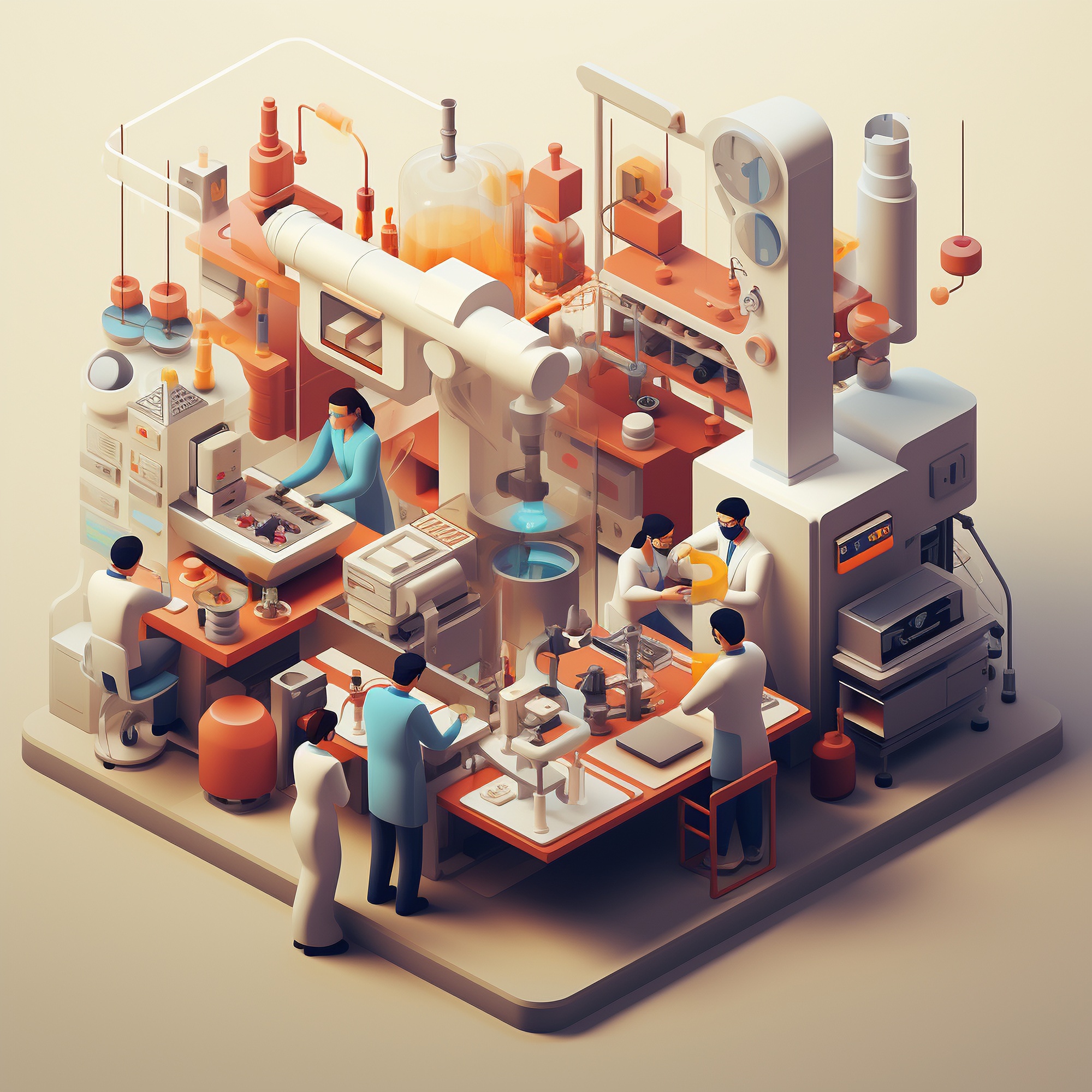
Machine calibration reduces the variability in production processes.
This, in turn, reduces the likelihood of product defects and ensures that products are manufactured to tight tolerances.
Prevention of Downtime
Prevention of Downtime

Regular machine maintenance and calibration can help identify and address potential issues before they lead to equipment breakdown or downtime.
Downtime can be costly and disrupt production schedules, affecting product quality and delivery timelines.
Extended Machine Lifespan
Extended Machine Lifespan
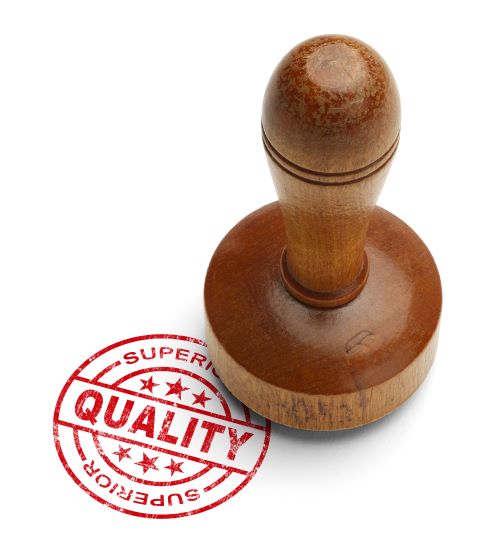
Proper maintenance can extend the lifespan of manufacturing equipment.
Replacing or repairing machines less frequently helps maintain consistency in production processes and quality.
Cost Savings
Cost Savings
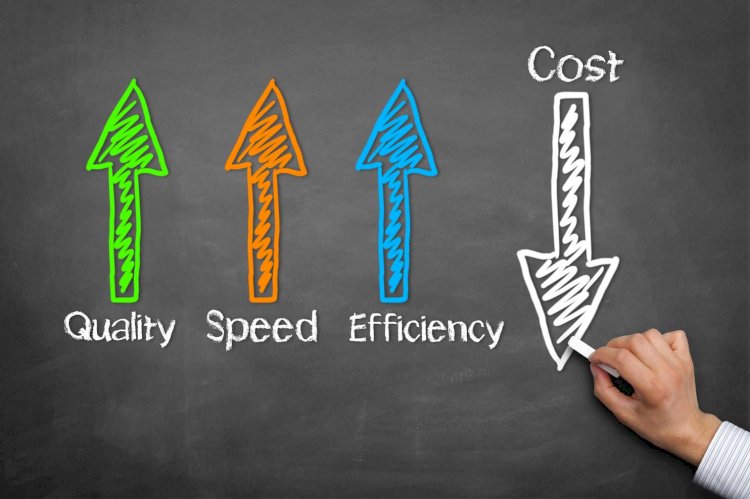
While machine calibration and maintenance have associated costs, they can ultimately lead to cost savings.
Fewer defects and rework mean less waste, reduced labor costs for fixing issues, and longer equipment lifespan, which all contribute to improved efficiency and lower operational costs.
Employee Safety
Employee Safety

Well-maintained machines are safer to operate.
Employee safety is an essential component of quality assurance, and avoiding accidents and injuries is vital for both ethical and business reasons.
Customer Satisfaction
Customer Satisfaction
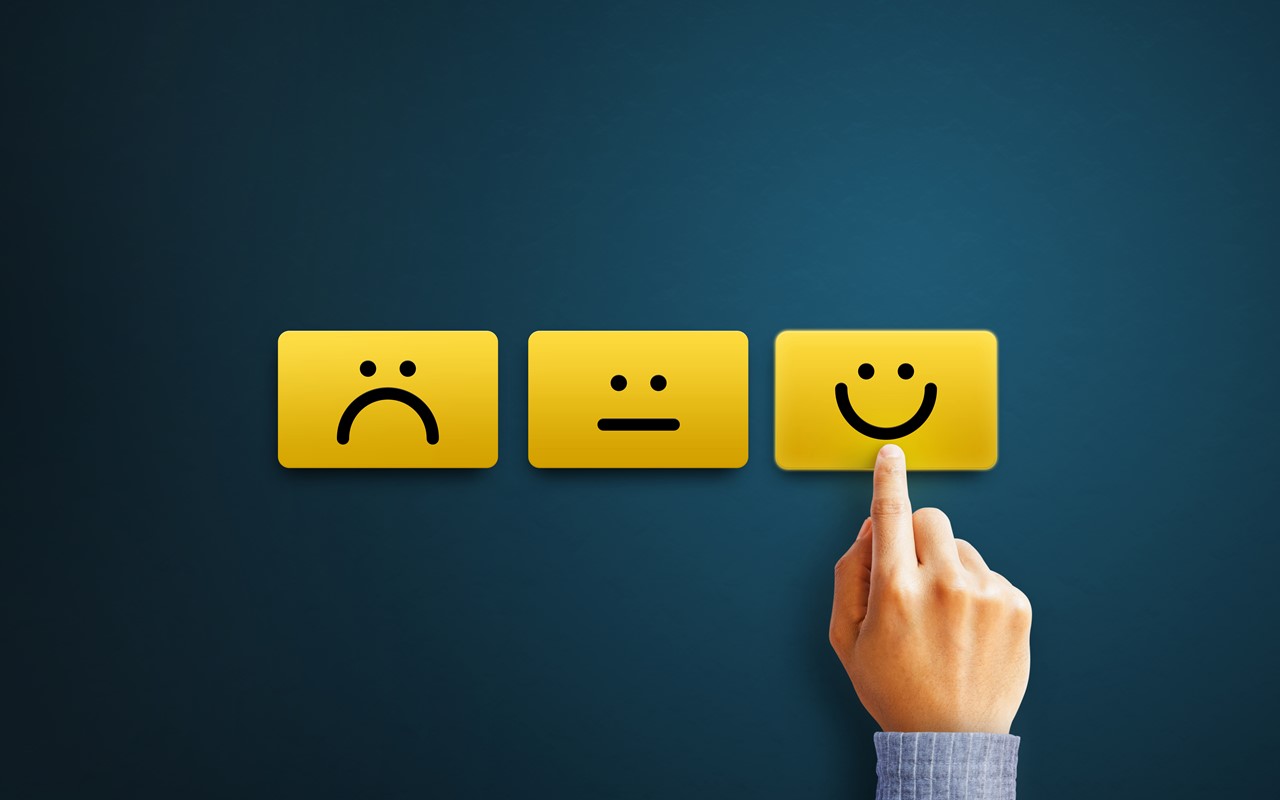
Ultimately, the products that result from well-calibrated and well-maintained machines are more likely to meet customer requirements, leading to higher customer satisfaction and repeat business.
Risk Mitigation
Risk Mitigation
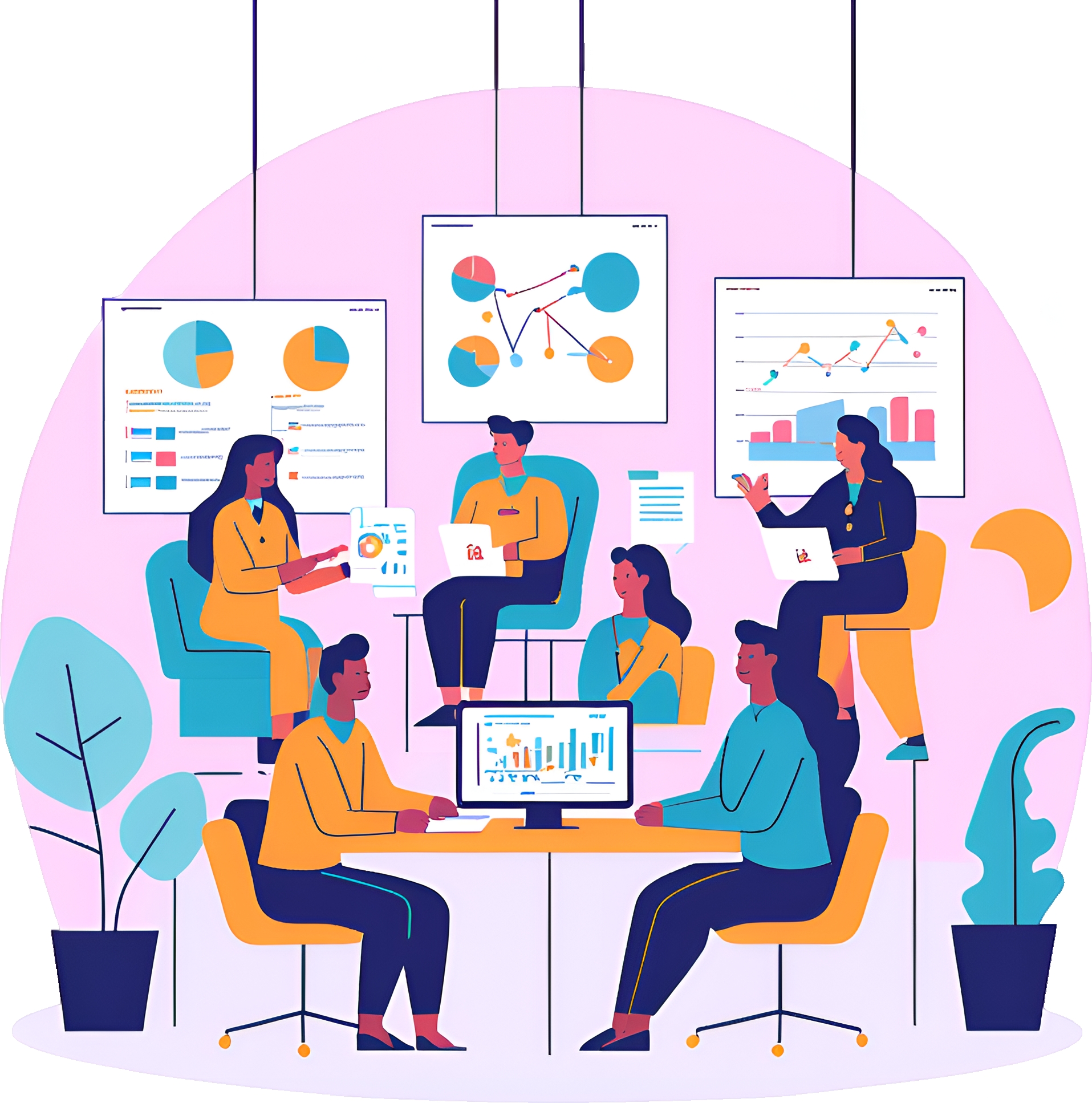
Proper calibration and maintenance reduce the risk of unexpected failures or deviations in the manufacturing process.
This mitigates the potential for costly product recalls, reputation damage, and legal issues.
In summary, machine calibration and maintenance are critical for maintaining consistent product quality, complying with regulations, reducing variability, and ensuring the reliability and efficiency of manufacturing processes. By investing in these practices, manufacturers can enhance their quality control and assurance efforts, leading to higher-quality products and a more competitive position in the market.